Here's some info for those of you interested in getting rid of those wimpy M10 head studs, and putting some big, meaty M12 studs in your motors. I'm not a fan of upgrading from M10 to the 7/16" hardware because there's simply not enough "meat" left in the 10mm stud bore to drill & retap to 7/16". If 7/16" hardware is going to be used, it should be installed in the block with a Helicoil or Timesert kit.
These are ARP P/N 151-4201 studs, and they're intended for a Ford Pinto. Their OAL is 116.87mm, and they have an M12x1.75 thread on the block side, and a M12x1.25 thread on the nut side; unfortunately there's only 25mm of thread on both sides (I know the nut side looks like it has more thread, but it's an illusion):
81.26mm sticking out of the block:
Now if you've done the math, you may be wondering how did we get 116.87 - 81.26 = 35.61mm of stud in the block with only 25mm of thread? Well, we cheated, and put a 0.500" counterbore 11mm deep in the block to "sink" them in:
It's really unfortunate that ARP didn't put longer threads on these, but after all, they were designed for the Pinto iron block application; I've been in touch with them to see about modifying this existing design to add another 10mm or so of thread for our ally blocks. We'll see what they say.....
As a point of interest, the bores for these studs can go
really deep without hitting the water jackets:
Other mods necessary to make these big studs work are enlarging the holes in the head, and enlarging the holes in the head gasket slightly, which we had Cometic do for us.
Once these are installed, since they're the standard 190,000 / 200,000 PSI ARP hardware the nuts "can" be torqued down to as much as 86 ft-lbs if ARP's moly lube is used. This is over twice as much clamping as the stock M10 fasteners and 30% more than 7/16"!
With this much clamping, the cylinders are going to be "pulled", so boring/honing with a torque plate is definitely a good idea.....
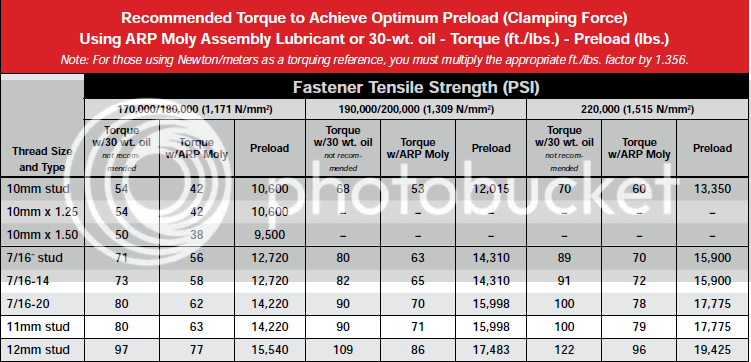