Sigh forum problems eating my posts!
What exactly are you welding??? Post your pics!
Use 1/16 and 3/32 filler until youre welding very thin metal. I preffer 3/32 on almost everything, but I can control it. Once you get use to thicker it's just easier. There's much less rod feeding to do with your off-hand and your skill increases alot I remember when I went from using 1/16 and mostly 3/32 at the house to 1/8, 5/32 and 5/16 rods. For an entire week I was lost. Once I got use to controlling it I got home and was a MUCH better welder.
Stainless welds almost exactly like MS once you get it. The only major differance is the chromium is sensative to the heat you're inputting, so you can't dilly dally all day like MS. The other differance (that I love) is that unlike MS. A stainless (within reason) will not run away and flow with gravity. It stays exactly how your arc orientates it.
Learn your electrode and filler angles.
One of the best first things you can do is google te electrode and filler angles for various positions and types of joints to be welded.
DITCH YOUR GAS CUPS FOR A GAS LENS SETUP
This will HALF the argon going through the torch, while allowing TREMENDOUS amounts of stick-out where you can see what you're doing. Also very helpful for doing restricted welds without a pencil torch.
Here's the flat out easyest way to learn to do stainless pipe.
The slowest you can practically weld it (giving you the most time to see what you are doing) is in pulse.
Set your machine to GTAW-P (tig-P) mode.
40amps
Balance too 20% high amp 80% low amp
Pule Per Second to 6 or 8 PPS
Start your arc with the pedal floored.
When the puddle is the wanted size dip your filler the first time.
Advance your arc and drop your heat from 100% to 75-80%.
From here continue the weld dipping, or walk the cup.
If you don't want to run pulse, start with 30amps.
The earlier you learn to walk the cup the better off you are!
Remember you're not getting paid $25-55/h to make 6GR welds. Your life will be made easier by keeping all pipe to pipe welds
uphill.
Stainless colors for two reasons. Chromium carbide precipitation, and poor shielding gas coverage. When you overheat stainless the chromium goes bye bye. Grossly overheated stainless is grey and is completely unacceptable. Mildly overheated are the pretty blue to purple tones. Poor gas coverage generally will be black.
It should seem obvious. Where there is color, there is a lack of chromium. The penalty for not brushing the "pretty ricer muffler colors" off is early rusting. All stainless exhaust welds need to be brushed clean after welding wth a stainless wire brush.
As he told you, a weld with nice gold bands around it lets you know that the heat is about right, and the gas coverage is good.
Now most manifold / exhaust welding is done between 18-gauge and Schedule-10 (.05-.109). This (and schedule-40) is fairly easly welded in one pass once you get the hang of it. I always one-pass with a correct root opening for my filler simply to save argon and stay in practice.
That being said 99% of people are there are going to two pass everything from 16 gauge and up by beveling the pipe, then running a cap pass. I suggest starting with that!
Stainless requires backpurging with argon, or solarflux-B. For yourown (or a buddies) work, no you do NOT have to backpurge even a turbo manifld. That being said do it when possible and NEVER sell non-backpurged welds. It's 2008; money welds get backpurged.
AFA the weld bead. Joining pipe to pipe with a butt or groove weld you want a flat, to convex profile (1/16". 1/8" max). Honestly... A nice bead will reinforce around 1/32" with all this thin pipe. With a fillet weld (say a slip joint, or weld to a flange) it CAN be concave, flat or convex PROVIDED the demensions from toe to toe and root to throat equal the thickness of the base material (or the smaller part)
The only real thing to grasp when you first weld anything beyond insensative mild steel is that heat isn't just amps. It's an average. It's an average of your arc's output VS the time it takes you to weld something.
One last thing. Clean the metal before welding. Check the filler and electrode for contamination BEFORE welding.
While you're welding the filler rod will cause impurities to float to the surface of the weld puddle. It'll be just a tiny dot that you carry along as you weld. If you keep it flowing around the middle of your puddle you travel speed (and hence your average heat input) is right on the money, and your angles are atleast fairly ballpark correct!
Alot of people ask how to walk the cup. And there's no really good way of telling people/grips without just showng them.
Theres an easy way to feed your filler rod and some grips on how to hold your torch to walk it.
When you walk the cup, you do not start by wlking the cup. You start by dipping th first dip or few then you transition into doing it to make it seamless. The electrode you simply run down the joint and hold pressure on it. Once you get the walking motion down pat it nearly welds itself.
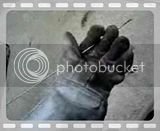