84pickup1uz
Fun Factor Garage - Canada Eh!
Ok guys..for those not following my build thread I am installing a 1st gen 1UZ motor in my 85 Pickup truck. I've decided it needs to be supercharged and I am using an Eaton 112. I'can't really afford to buy a manifold from down under so I am making one with the help of my local water jet company. Here is the 3D model of the top half of the manifold which will house the intercooler and get welded to the modifiied stock lower intake manifold. I hacked off the top of the runners and had it decked flat.
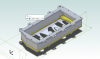
Anyone here have any advise for me? Pretty simple concept and I am sure I am not the first to do this.
The yellow layer is a composite spacer and I could make more of it from this material. I have hood clearance of 3" or 750mm. The stack is designed so I can interchagne the layer for the intercooler or even remove it.
What do you guys think?
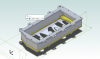
Anyone here have any advise for me? Pretty simple concept and I am sure I am not the first to do this.
The yellow layer is a composite spacer and I could make more of it from this material. I have hood clearance of 3" or 750mm. The stack is designed so I can interchagne the layer for the intercooler or even remove it.
What do you guys think?
Last edited: